By niuelec | 08 January 2025 | 0 Comments
From Design to Delivery: The Copper Connector Manufacturing Process
Copper connectors play a vital role in various industries, ensuring reliable and efficient connections for electrical systems. The manufacturing process for copper and brass connectors is crucial, as it determines the quality, performance, and durability of the final product. If you’re exploring top copper connector manufacturers or suppliers, understanding the process from design to delivery can help you identify the key differentiators that lead to superior products. This article takes you through the steps, highlighting the significance of material selection, precision manufacturing, quality assurance, and delivery management.
Material Selection and Its Role in Final Connector Quality
The foundation of a high-quality copper connector begins with material selection. A trusted copper connector manufacturer prioritizes the use of high-purity copper (such as CU with 99.9% purity) to ensure excellent conductivity, durability, and resistance to corrosion. Brass connectors, composed of a combination of copper and zinc, offer additional flexibility in certain applications due to their mechanical strength and corrosion resistance. Selection doesn’t stop at base materials; dimensions are also considered meticulously, aligned with international standards or custom client requirements. The right material not only enhances functionality but also contributes to the longevity of the electrical system where the connector will be used. Selecting premium materials can distinguish the end product from competitors' offerings, ensuring compatibility with diverse industrial applications.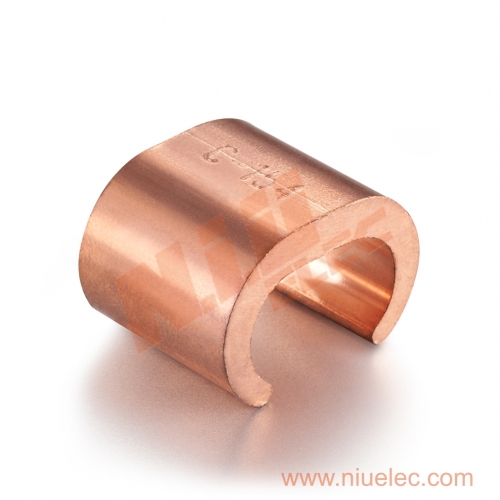
How Precision Manufacturing Improves Performance Reliability
Once materials are selected, the manufacturing process is where copper connectors take shape. Precision engineering and advanced technology are central to creating connectors that deliver consistent, reliable performance. Techniques like stamping, crimping, and machining are used to craft copper or brass connectors to precise tolerances. A leading copper connector supplier will integrate automated systems into production lines, minimizing human error and enhancing efficiency. The importance of accurate shaping, exact dimensions, and proper crimping processes cannot be overstated; small deviations can lead to poor conductivity or mechanical issues. Leveraging state-of-the-art technology allows for the manufacturer to provide uniform connectors that meet rigorous testing for conductivity and durability, solidifying their reliability for use in demanding electrical environments.Steps to Ensure On-Time Delivery Without Sacrificing Quality
For any copper connector manufacturer, maintaining a balance between meeting delivery deadlines and upholding quality is critical. The production schedule starts with effective planning, ensuring raw material procurement aligns with order timelines. Throughout the manufacturing process, quality inspections serve as checkpoints, verifying that connectors meet the specified standards at each stage. From prototype evaluation to batch testing, no detail is overlooked. Additionally, using advanced logistics systems helps optimize the supply chain, enabling seamless delivery to customers. A top-tier copper connector supplier deploys clear communication channels with clients, providing real-time updates on shipment status. These practices ensure that businesses receive their products as promised without compromising the integrity of the connectors, enhancing client satisfaction and operational efficiency.Key Differentiators Among Top Copper Connector Suppliers
With numerous suppliers in the market, identifying a trusted copper connector supplier lies in recognizing key differentiators. Ethical sourcing of high-quality materials ensures superior connectors, while certifications like ISO standards indicate a commitment to quality management systems. Suppliers who offer customization options stand out, as they can adapt connectors to specific project requirements. Technological advancements in manufacturing processes, coupled with comprehensive testing capabilities, further validate the reliability and durability of the products. Suppliers with transparent policies on delivery, customer support, and post-purchase guidance add immense value to their partnerships. Ultimately, a reliable supplier will not only meet but exceed expectations by delivering consistently high-performing connectors that cater to various industrial applications.The transition from design to delivery in copper connector manufacturing reflects a seamless combination of material expertise, precision engineering, and strategic logistics. These connectors, such as the CCT C-Type Copper Connector, ensure optimal performance in diverse environments through uncompromising quality. Whether you require copper connectors with specific dimensions or brass connectors for robust applications, selecting a supplier that excels across every stage of the process guarantees a reliable and efficient solution. When choosing your next copper connector supplier, prioritize those who emphasize high-purity materials, advanced manufacturing technologies, rigorous testing, and strategic delivery management.
Leave a Reply
Your email address will not be published.Required fields are marked. *
CATEGORIES