By niuelec | 16 April 2025 | 0 Comments
Beyond the Initial Price Tag: How Durable Cable Connectors Drive Sustainability and Long-Term Saving
In today's industrial landscape, the pressure is mounting. Businesses face the dual challenge of optimizing operational efficiency while simultaneously demonstrating a tangible commitment to environmental sustainability. Often, the focus falls on large-scale initiatives – renewable energy adoption, waste reduction programs, or supply chain optimization. However, significant gains can often be found in the details, specifically in the components that form the backbone of electrical and electronic systems. Cable crimp connectors, especially those from trusted copper connector manufacturers, play a critical role. Choosing connectors based solely on initial cost can lead to a cascade of hidden expenses and environmental burdens down the line. Conversely, prioritizing durability isn't just about longevity; it's a strategic decision that directly translates into reduced resource consumption, lower maintenance costs, and enhanced operational reliability – a win-win for both the balance sheet and the planet. This exploration delves into why durable cable connectors are an essential element of modern, sustainable industrial practices.
Table of contents:
Material Matters: The Foundation of Longevity
Engineered for Endurance: The Role of Structural Design
Extending the Lifecycle: A Long-Term Perspective on Savings
Resource Conservation: More Than Just Metal
Delivering Enduring Value: Benefits Across the Chain
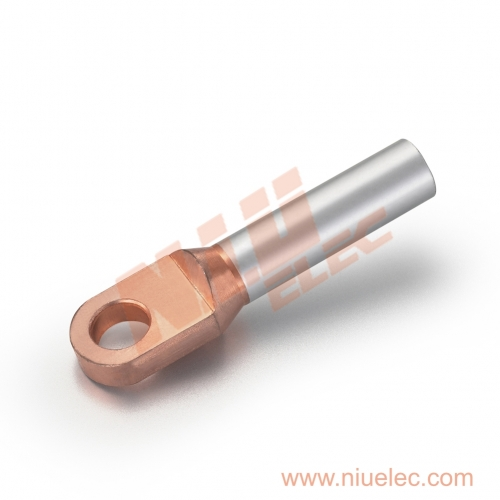
The humble cable crimp connector, often overlooked, offers significant economic and environmental benefits. Focusing beyond the initial purchase price highlights the importance of durability for long-term efficiency and sustainability. Choosing connectors made with high-strength materials like aluminum, precision engineering, and a focus on lifecycle performance can drastically reduce replacement frequency. This lowers total ownership costs through savings in labor, downtime, and logistics, while conserving resources, minimizing waste, and reducing the carbon footprint tied to manufacturing and transportation.Achieving these benefits requires partnering with manufacturers who prioritize longevity and resource efficiency. Companies like N.I.U ELEC design Cable Crimp Connectors with durability as a core principle, delivering solutions that enhance reliability while supporting environmental goals. Choosing durable connectors isn’t just an option—it’s a strategic investment in building a more sustainable future.
Table of contents:
Material Matters: The Foundation of Longevity
Engineered for Endurance: The Role of Structural Design
Extending the Lifecycle: A Long-Term Perspective on Savings
Resource Conservation: More Than Just Metal
Delivering Enduring Value: Benefits Across the Chain
Material Matters: The Foundation of Longevity
The lifespan and reliability of a cable connector begin at the most fundamental level: the material it's made from. The choice of material dictates its resistance to environmental stressors, its structural integrity over time, and ultimately, how frequently it will need replacement.- The Power of High-Strength Aluminum: While various metals are used in connector manufacturing, high-strength aluminum alloys offer compelling advantages in specific demanding applications. Notably, their inherent resistance to corrosion is a significant factor. In environments characterized by high humidity, salinity (coastal or marine applications), or exposure to industrial chemicals, connectors made from inferior materials can quickly succumb to rust and degradation. This corrosion not only compromises the physical structure but also degrades electrical performance, leading to potential failures and mandatory replacement. High-quality aluminum alloys, however, form a protective oxide layer, enabling them to withstand these harsh conditions for extended periods. This makes them exceptionally well-suited for long-term outdoor installations, renewable energy infrastructure, and challenging industrial settings where longevity is paramount.
- Structural Stability and Aging: Beyond corrosion, the inherent stability of the chosen material plays a crucial role in combating structural aging. Connectors are subjected to mechanical stress during installation (crimping) and throughout their operational life due to vibration, temperature fluctuations, and physical handling. High-quality materials, engineered for stability, resist deformation, micro-fractures, and embrittlement over time. This ensures the connector maintains its structural integrity and clamping force, preventing intermittent connections or complete failures that necessitate premature replacement.
- Comparative Lifespan Analysis: When compared to some commonly used materials like basic steel or certain grades of brass, carefully selected and treated high-strength aluminum alloys can offer superior longevity, particularly in corrosive environments. While copper is an excellent conductor often sought after (many search for a reliable Copper connector supplier for this reason), specialized aluminum alloys can provide a better balance of durability, weight, and corrosion resistance for specific structural and environmental challenges. The decision isn't always about conductivity alone, but the holistic performance over the entire lifecycle. Choosing materials specifically for their endurance characteristics reflects a deeper commitment to reducing the replacement cycle, which is inherently more sustainable. Less frequent replacement means less mining, refining, and processing of raw materials over the operational lifespan of the equipment or installation.
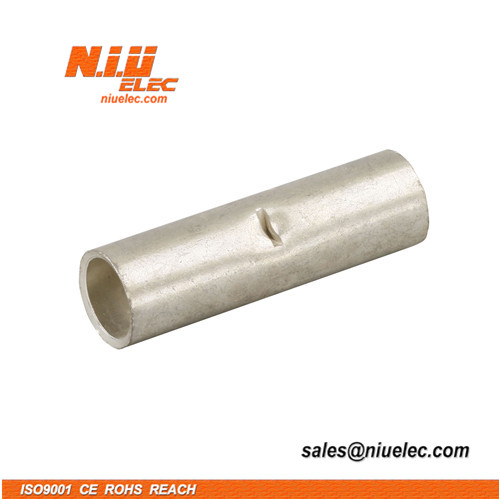
Engineered for Endurance: The Role of Structural Design
Material choice lays the groundwork, but sophisticated structural design transforms potential longevity into reliable performance. The way a connector is engineered directly impacts its ability to form and maintain a secure, low-resistance connection, minimizing the need for maintenance and replacement.- Precision Interfaces (DIN Standards): Adherence to established standards, such as DIN 74 for certain connector types, signifies a commitment to precision engineering. These standards dictate critical dimensions and tolerances for the connector's interface. A precisely manufactured interface ensures a snug, secure fit with the corresponding terminal or conductor. This high degree of fit minimizes the potential for micro-movements caused by vibration or thermal cycling, which can lead to loosening, increased contact resistance, heat generation (hot spots), and potentially dangerous electrical arcing. A connection that stays tight requires less frequent inspection and eliminates failures caused by poor mechanical fit, thereby extending its useful life and reducing associated maintenance labor.
- Mechanically Robust Crimping Zones: The crimp area is where the connector physically joins the cable conductor. The design of this zone is critical for long-term reliability. Connectors engineered with high mechanical strength in the crimping barrel ensure a solid, gas-tight connection when properly crimped. This robust design withstands the significant forces applied during installation without cracking or deforming excessively. More importantly, it maintains consistent pressure on the conductor strands over time, preventing strand breakage, pull-out, or the ingress of moisture and contaminants that could degrade the connection. A strong, reliable crimp is fundamental to preventing electrical failures and the subsequent need for connector replacement.
- Adaptability and Waste Reduction: Connectors designed with broad adaptability for various cable sizes or types within a specified range offer another subtle sustainability advantage. Using a connector that can reliably accommodate slightly different conductor diameters or insulation thicknesses (within its rated capacity) reduces the likelihood of using an incorrectly sized part, which can lead to poor connections or wasted components. It also simplifies inventory management for large projects, reducing the number of SKUs needed and minimizing potential obsolescence or waste due to specification changes.
Extending the Lifecycle: A Long-Term Perspective on Savings
The true value of a durable connector emerges when viewed through the lens of its entire lifecycle. Focusing solely on the upfront purchase price ignores the substantial downstream costs associated with frequent replacements.- Comparing Replacement Cycles: Consider a typical industrial application. Standard, lower-quality connectors might require inspection and potential replacement every few years, or even more frequently in harsh environments. In contrast, a high-durability connector, built with superior materials and design, could realistically last significantly longer, perhaps matching the lifespan of the equipment itself. Quantifying this difference – comparing the average replacement cycle of standard connectors versus the extended lifespan of premium ones – reveals a compelling economic argument.
- Cumulative Cost Savings (Beyond the Part): Each replacement event incurs costs far exceeding the price of the connector itself. These include:
-
- Labor: Technicians' time for diagnostics, removal, and installation.
- Downtime: Lost production or operational capability while repairs are made.
- Logistics: Transportation costs for new parts and potentially for personnel.
- Materials: The cost of the replacement connector and any associated consumables.
When multiplied over hundreds or thousands of connection points in a large facility or project, and repeated over several replacement cycles avoided, the cumulative savings become substantial. This Total Cost of Ownership (TCO) perspective clearly favors durable components.
- Reducing Rework and Project Delays: In major engineering or construction projects, connector failures during commissioning or early operation can lead to costly rework and significant delays. Using connectors known for their reliability from the outset minimizes this risk. Imagine the impact on a renewable energy farm or a manufacturing plant rollout if dozens of connections fail prematurely – the troubleshooting effort and schedule disruption can dwarf the initial cost difference of using higher-quality components. Durability translates directly into project certainty and reliability.
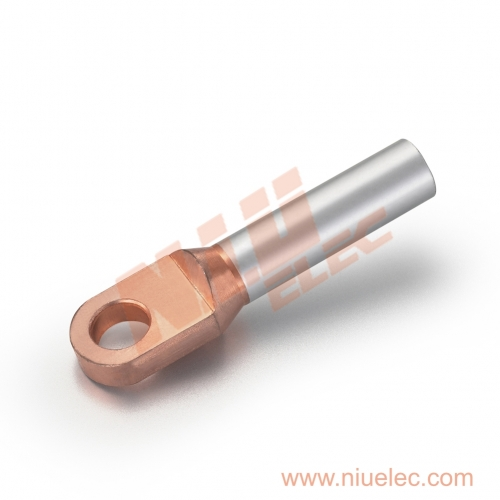
Resource Conservation: More Than Just Metal
The environmental benefits of durable connectors extend beyond simply using less raw material over time. Reducing the replacement frequency triggers a positive cascade effect across multiple resource streams.
- Reduced Manufacturing Footprint: Every connector produced requires energy for extraction, processing, manufacturing, and finishing. Fewer replacements mean significantly less cumulative energy consumption and fewer associated emissions (greenhouse gases, pollutants) from the manufacturing process over the system's lifetime. It also means less scrap metal generated during production and disposal.
- Minimized Packaging Waste: Connectors are typically packaged for protection and identification. While necessary, packaging contributes to waste streams. Halving the number of replacements needed directly halves the associated packaging waste (cardboard, plastic) generated over the operational period.
- Lower Transportation Emissions: Fewer replacement cycles directly translate into fewer transportation runs needed to deliver new components to site, especially critical for large-scale industrial projects or geographically dispersed infrastructure. This reduction in logistics activity lowers the overall carbon footprint associated with maintenance and upkeep.
- Enhanced Energy Efficiency: Poor or degrading connections exhibit higher electrical resistance. This resistance leads to energy loss in the form of heat (I²R losses) and can cause voltage drops, potentially affecting equipment performance. Stable, low-resistance connections maintained over long periods thanks to durable connectors contribute to overall system energy efficiency, reducing operational energy waste.
Delivering Enduring Value: Benefits Across the Chain
The adoption of durable cable connectors delivers tangible value not just environmentally, but also strategically to businesses and their customers.
- Lower Maintenance Burden for Bulk Users: For Original Equipment Manufacturers (OEMs) or system integrators managing large fleets of equipment or extensive installations, extending the maintenance cycle of components like connectors directly reduces their ongoing service and warranty costs. This translates into improved profitability and potentially more competitive service offerings.
- Alignment with Sustainability Trends: Increasingly, industries are facing regulatory pressure and market demand for environmentally responsible products and operations. Specifying and using durable components that minimize waste aligns with corporate sustainability goals and meets the growing expectation for eco-certified or environmentally conscious industrial parts. Companies are actively seeking suppliers, including searching for a responsible Copper connector manufacturer or providers of other durable material alternatives, who can support these initiatives.
- Enhanced Brand Reputation: Companies that prioritize high-quality, durable components signal a commitment to reliability and long-term value. Choosing suppliers known for their durable and environmentally considered products can enhance the end-user's brand image, positioning them as responsible and quality-focused entities within their own markets. It demonstrates a commitment that goes beyond the surface level, embedding sustainability into the very fabric of their operations.
The humble cable crimp connector, often overlooked, offers significant economic and environmental benefits. Focusing beyond the initial purchase price highlights the importance of durability for long-term efficiency and sustainability. Choosing connectors made with high-strength materials like aluminum, precision engineering, and a focus on lifecycle performance can drastically reduce replacement frequency. This lowers total ownership costs through savings in labor, downtime, and logistics, while conserving resources, minimizing waste, and reducing the carbon footprint tied to manufacturing and transportation.Achieving these benefits requires partnering with manufacturers who prioritize longevity and resource efficiency. Companies like N.I.U ELEC design Cable Crimp Connectors with durability as a core principle, delivering solutions that enhance reliability while supporting environmental goals. Choosing durable connectors isn’t just an option—it’s a strategic investment in building a more sustainable future.
Leave a Reply
Your email address will not be published.Required fields are marked. *
CATEGORIES