By niuelec | 23 February 2024 | 0 Comments
Leveraging Insulation Piercing Connectors for Improved Electrical Connections
In the realm of secure and efficient electrical connections, one component has steadily gained recognition for its contributions to safety, convenience, and performance: the insulation piercing connector (IPC). These devices offer a marked improvement over traditional methods of securing electrical connections, especially in environments where precision and reliability are non-negotiable.
Understanding the nuances of IPC usage, the benefits they offer, and future applications can empower electrical professionals with the knowledge necessary to achieve optimal results in their installations.
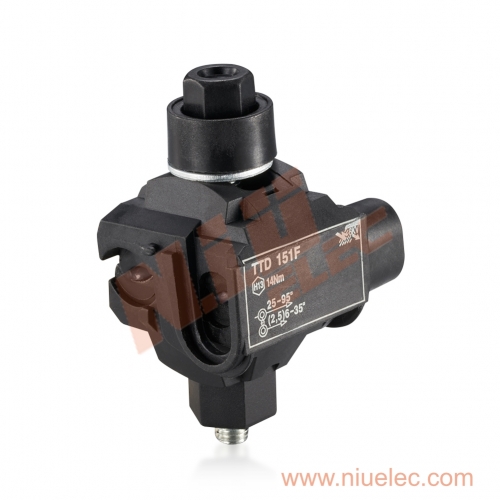
Understanding the nuances of IPC usage, the benefits they offer, and future applications can empower electrical professionals with the knowledge necessary to achieve optimal results in their installations.
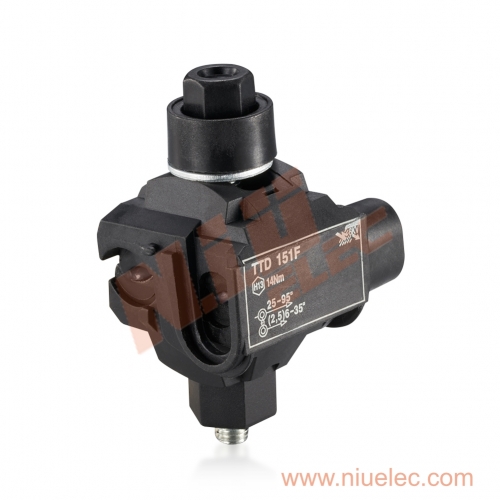
The Basics of Insulation Piercing Connectors: What You Need to Know
Insulation piercing connectors (IPCs) are a unique type of connector used in electrical wiring to make a tap or splice without needing to cut or strip the wire’s insulation. This means that not only do IPCs provide a secure electrical connection, but they also ensure that the electrical circuit remains unaffected by any external damage to the insulation.
They are designed with sharp or pointed contacts that can penetrate through the insulation and make contact with the inner conductor, establishing a secure and conductive path. IPCs come in a variety of shapes and sizes, suitable for different types and thicknesses of insulation materials, from polyethylene and rubber to cross-linked polyolefin (XLPE).
Manufacturers like NiuElec have developed IPCs that employ a spring-loaded mechanism and silver-plated materials to ensure a reliable and low-resistance connection, meeting strict industry standards for power distribution and telecommunications applications.
Advantages of Using Insulation Piercing Connectors in Electrical Installations
The benefits of using IPCs in electrical installations are multifaceted. They provide a range of advantages that address common concerns related to traditional connection methods, including labor intensiveness, reliability, and installation convenience.
A significant advantage of IPCs is their ability to reduce installation time and complexity. Their mechanism allows for quick and easy connections without the need for stripping wire insulation, saving time and ensuring that installations are carried out more rapidly.
Another notable benefit is the enhanced safety they provide. By eliminating the need to strip insulation, IPCs reduce the likelihood of accidental electrical shorts or human error, a common issue with traditional connection methods.
In addition, IPCs can maintain a waterproof seal on the connected wires, a crucial feature for outdoor or submersible applications, where protecting against moisture and environmental contaminants is imperative.
Case Studies: How Insulation Piercing Connectors Improve Connection Quality
Case studies reveal powerful examples of how IPCs have revolutionized connection quality across various applications. For instance, in the field of street lighting, where connections are often exposed to the elements, IPCs have significantly increased the longevity and reliability of electrical joints.
In the telecommunications sector, IPCs have facilitated the rapid and precise connection of wires, enabling faster signal transmission and minimizing signal loss due to reduced resistance in the electrical paths.
These case studies underscore how IPCs offer a solution to the specific challenges in different industries, demonstrating their adaptability and effectiveness in diverse environments.
Expert Tips for Properly Installing and Using Insulation Piercing Connectors
To make the most of IPCs, it’s essential to follow best practices for installation. Electrical professionals should first choose the right IPC for the application, considering factors such as wire gauge, insulation type, and the number of potential tap points.
Proper preparation of the wires is key, as consistent wire stripping can ensure a good and clean pierce. During installation, maintaining a 90-degree angle and line pressure will lead to the desired penetration without damaging the conductor inside.
Post-installation, experts recommend testing the connection for continuity and stability to ensure it meets performance expectations.
The Future of Electrical Connections: The Role of Insulation Piercing Connectors
As technology advances, the role of IPCs in improving electrical connections will become even more pronounced. With the increasing prominence of smart grids and the Internet of Things (IoT), the demand for secure, long-lasting, and efficient electrical connections will only grow.
In the not-so-distant future, IPCs with built-in smart functionalities, or those designed specifically for high-frequency applications, could become the norm. These advancements will not only enhance the integrity of connections but also help systems achieve greater efficiency and responsiveness.
Controlled testing and use in new applications will continue to uncover new benefits and further cement the position of IPCs as an indispensable component in modern electrical engineering.
Insulation piercing connectors represent an exciting area of innovation within the electrical industry, offering improved solutions over conventional connection methods across various sectors. By understanding their applications, advantages, and proper use, professionals can harness the full potential of IPCs to create more reliable and efficient electrical systems.
To explore IPCs further, visit NiuElec's website, where a range of specialized connectors designed for different applications are available for technical specification and inquiry.
Insulation piercing connectors (IPCs) are a unique type of connector used in electrical wiring to make a tap or splice without needing to cut or strip the wire’s insulation. This means that not only do IPCs provide a secure electrical connection, but they also ensure that the electrical circuit remains unaffected by any external damage to the insulation.
They are designed with sharp or pointed contacts that can penetrate through the insulation and make contact with the inner conductor, establishing a secure and conductive path. IPCs come in a variety of shapes and sizes, suitable for different types and thicknesses of insulation materials, from polyethylene and rubber to cross-linked polyolefin (XLPE).
Manufacturers like NiuElec have developed IPCs that employ a spring-loaded mechanism and silver-plated materials to ensure a reliable and low-resistance connection, meeting strict industry standards for power distribution and telecommunications applications.
Advantages of Using Insulation Piercing Connectors in Electrical Installations
The benefits of using IPCs in electrical installations are multifaceted. They provide a range of advantages that address common concerns related to traditional connection methods, including labor intensiveness, reliability, and installation convenience.
A significant advantage of IPCs is their ability to reduce installation time and complexity. Their mechanism allows for quick and easy connections without the need for stripping wire insulation, saving time and ensuring that installations are carried out more rapidly.
Another notable benefit is the enhanced safety they provide. By eliminating the need to strip insulation, IPCs reduce the likelihood of accidental electrical shorts or human error, a common issue with traditional connection methods.
In addition, IPCs can maintain a waterproof seal on the connected wires, a crucial feature for outdoor or submersible applications, where protecting against moisture and environmental contaminants is imperative.
Case Studies: How Insulation Piercing Connectors Improve Connection Quality
Case studies reveal powerful examples of how IPCs have revolutionized connection quality across various applications. For instance, in the field of street lighting, where connections are often exposed to the elements, IPCs have significantly increased the longevity and reliability of electrical joints.
In the telecommunications sector, IPCs have facilitated the rapid and precise connection of wires, enabling faster signal transmission and minimizing signal loss due to reduced resistance in the electrical paths.
These case studies underscore how IPCs offer a solution to the specific challenges in different industries, demonstrating their adaptability and effectiveness in diverse environments.
Expert Tips for Properly Installing and Using Insulation Piercing Connectors
To make the most of IPCs, it’s essential to follow best practices for installation. Electrical professionals should first choose the right IPC for the application, considering factors such as wire gauge, insulation type, and the number of potential tap points.
Proper preparation of the wires is key, as consistent wire stripping can ensure a good and clean pierce. During installation, maintaining a 90-degree angle and line pressure will lead to the desired penetration without damaging the conductor inside.
Post-installation, experts recommend testing the connection for continuity and stability to ensure it meets performance expectations.
The Future of Electrical Connections: The Role of Insulation Piercing Connectors
As technology advances, the role of IPCs in improving electrical connections will become even more pronounced. With the increasing prominence of smart grids and the Internet of Things (IoT), the demand for secure, long-lasting, and efficient electrical connections will only grow.
In the not-so-distant future, IPCs with built-in smart functionalities, or those designed specifically for high-frequency applications, could become the norm. These advancements will not only enhance the integrity of connections but also help systems achieve greater efficiency and responsiveness.
Controlled testing and use in new applications will continue to uncover new benefits and further cement the position of IPCs as an indispensable component in modern electrical engineering.
Insulation piercing connectors represent an exciting area of innovation within the electrical industry, offering improved solutions over conventional connection methods across various sectors. By understanding their applications, advantages, and proper use, professionals can harness the full potential of IPCs to create more reliable and efficient electrical systems.
To explore IPCs further, visit NiuElec's website, where a range of specialized connectors designed for different applications are available for technical specification and inquiry.
Leave a Reply
Your email address will not be published.Required fields are marked. *
CATEGORIES